オイル分析は何に役立つ!?
ホワイトメタルの焼き付き
航空機の分野では分解点検がかえって故障の原因となる場合があるという事実から、分解せずにエンジン内部の摩耗状態を監視し、不必要な分解点検を避ける目的でアメリカで開発された手法がSOAP法です。現在は、一般産業用の設備診断にも広く利用されています。
摩耗粒子の金属元素はそのまま摩耗部位を示し、その量の増加は異常摩耗(損傷)を意味します。従って、定期分析による各金属元素の量のトレンドを見ていけば、どこの部位がどの様な摩耗状態にあるかを推測できます。
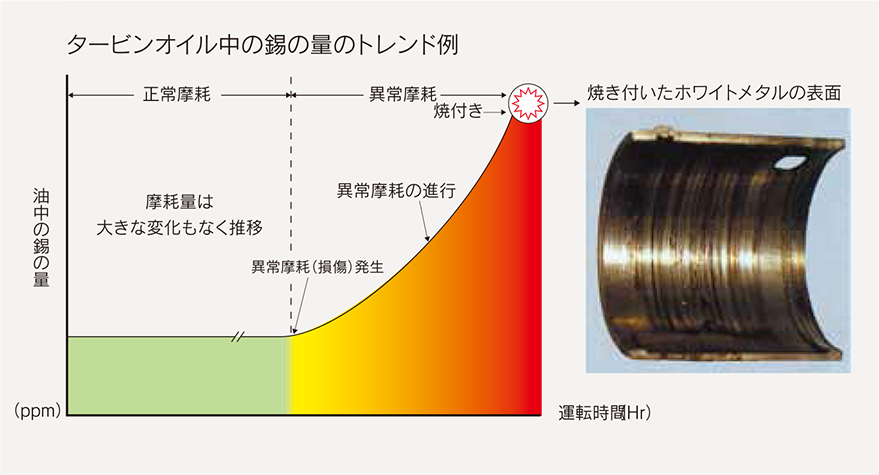
造管ギアボックスの異常摩耗の発見
20年以上も日曜以外24時間稼働の平板からパイプを作る円筒曲げ加工機のウォームギヤで異常摩耗を発見した例です。従来振動を診ながら定期更油で保全していましたが、オイル分析を適用したところ、振動法では異常はありませんでしたが、特にDRフェログラフィのデータに異常がみられたため、ギヤボックスを開放点検しました。
その結果、歯面全体に条痕がみられ、スポーリングのピットもありました。その後、この異常摩耗時のDRフェログラフィの摩耗強度指数を管理基準値に設定し、他の同様な造管ラインにもこれを適用し、計画保全を展開し、保全費・部品交換コストの削減に貢献しています。
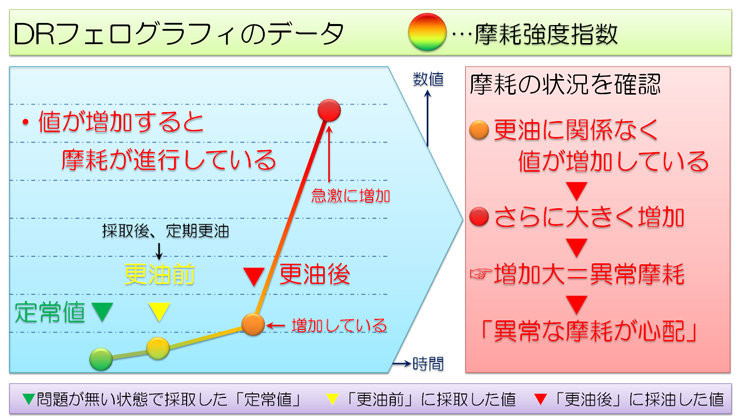
LPG車の更油期間の延長
ある陸送会社における2車種の3カ月後の潤滑油分析結果を対比した事例です。この会社では数百台のLPG車に対して3カ月毎に整備・点検を行い、同時に潤滑油を新油に入れ替えています。事例のA車の潤滑油はかなり劣化していて入れ替えは妥当ですが、B車の方は必要ないと考えられます。
B車だけでも入れ替えなければその経済効果として、整備・点検時間の低減、LPG車の稼働率の向上および潤滑剤コストの削減が期待できます。
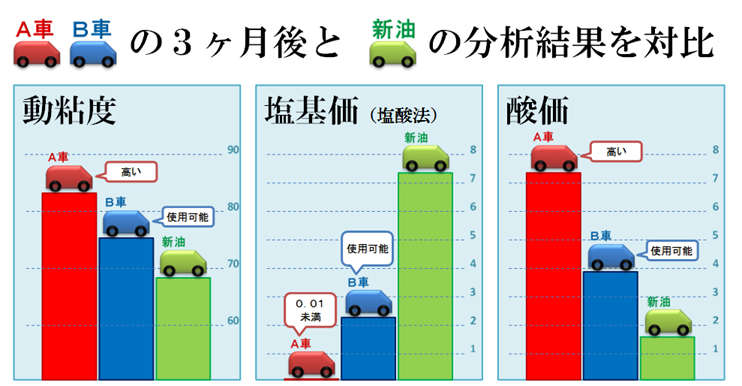